Production Practical Steps of Woven Bags
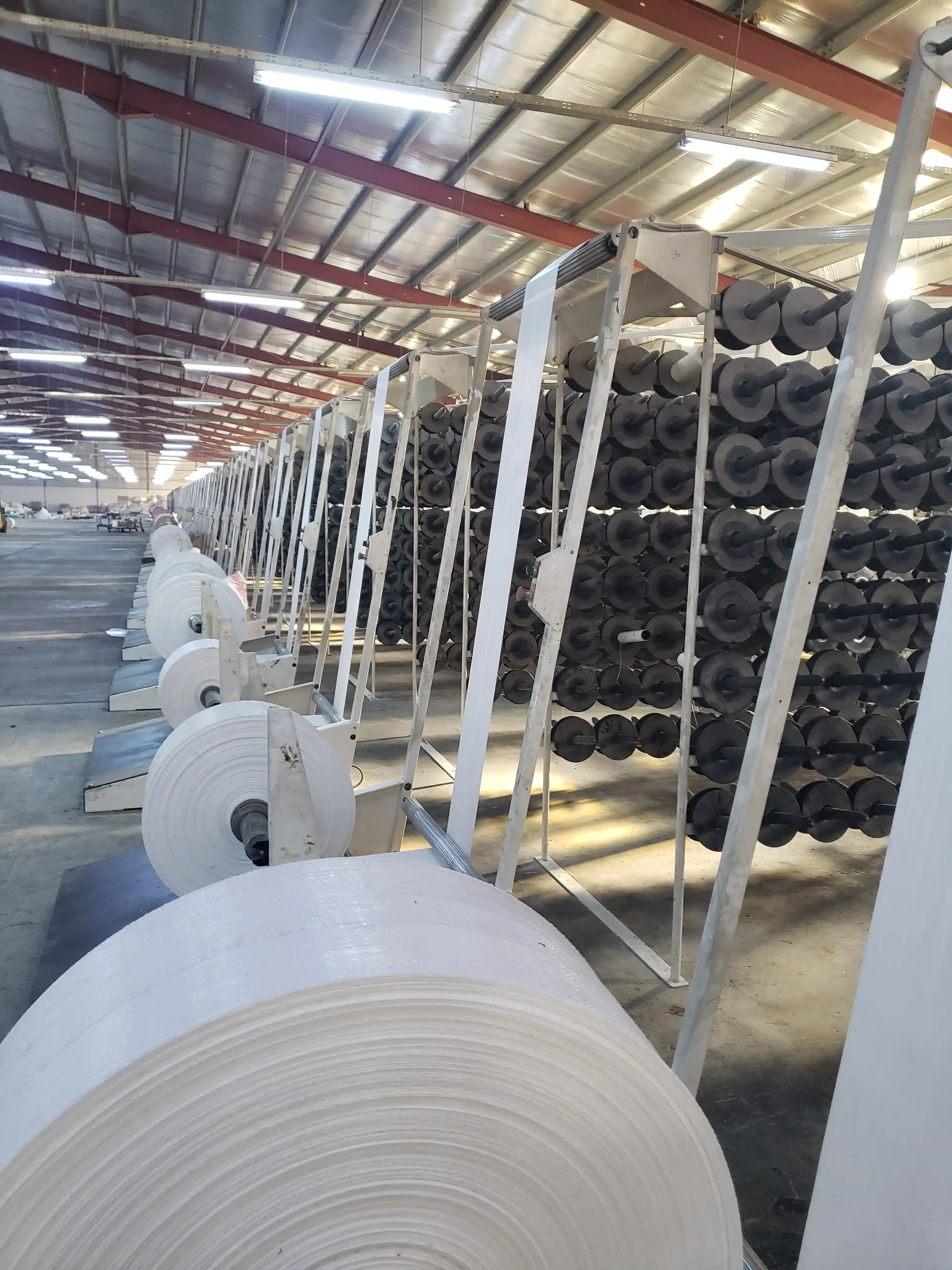
Step One
The thread production phase using the Starex thread line is one of the latest thread manufacturing technologies, imported from Aster Linger, one of the world's leading companies in this field. The line features advanced technologies including automatic mixing devices that precisely adjust the mixing ratios on demand, as well as a computer system that allows complete control of the thread specifications ensuring high-quality production. Productive process steps:
1. Pour raw materials, include polypropylene, calcium carbonate, masterbatch and recycled materials, into custom tanks.
2. Adjust the raw material mixing ratios to the required specifications, as the mixing is automatic to ensure the perfect homogenization process.
3. Heating raw materials by sophisticated heaters on the acryoder unit to turn them into molten state.
4. Propulsion of molten material by a rotary screw (ESCROW) to the mold unit (DIY) to form the film and then pass it in a cold water basin to cool it.
5. Tighten the film after cooling through the tensile unit, where it is cut by the solos unit.
6. Heat the threads through the first rolls and then in an oven with a temperature of up to 160 ° C for the tensile process (Stretching).
7. Adjust the thread width from the initial case to the final presentation required.
8. Wrap the finished threads on rollers, whether as Warp or weft.
These steps are produced high quality threads that meet various specifications and needs.
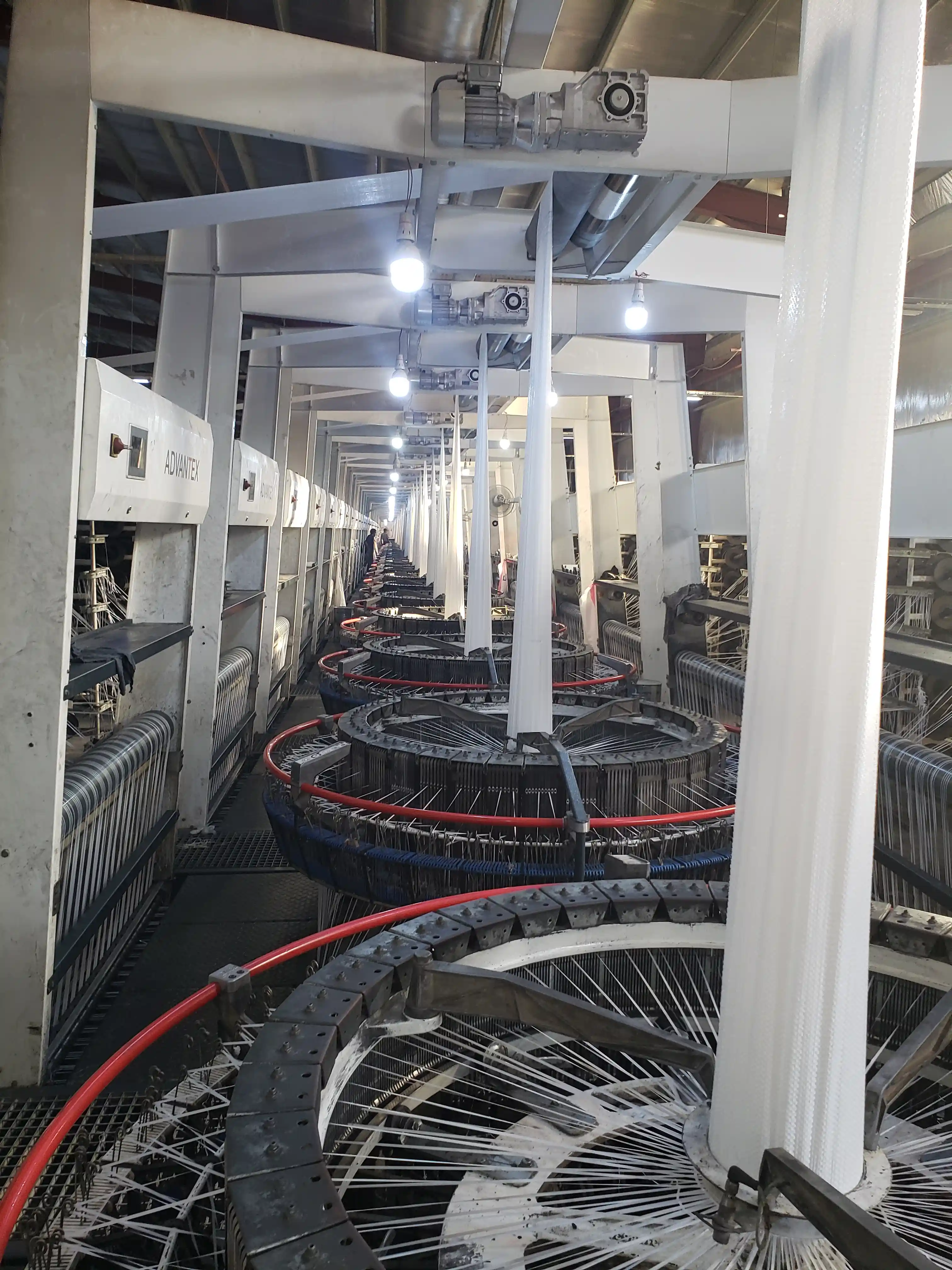
Step Two
The loose phase at this stage the threads are converted into tissue using a virgin composite on pregnant women called Warp suction. Dam threads are distributed in a computational manner depending on the width of the fabric and the dam density required for the bag, the process steps:
1. Dam threads pass through special combs.
2. Threads move to firefighters.
3. The threads reach the fabric collar to meet the weft threads installed in the knuckles.
4. When the loom rotates, the process of interference between the virgin of the saddle and the virgin of the weft is carried out.
5. The resulting fabric is pulled by drag rolls.
6. Wrap the fabric on a special roll.
7. The loom features a computer system that enables productivity control, careful follow-up to improve efficiency, and easily change the weft density according to demand.
8. When the fabric roll is filled it is cut and transferred to the next stage in the production process.
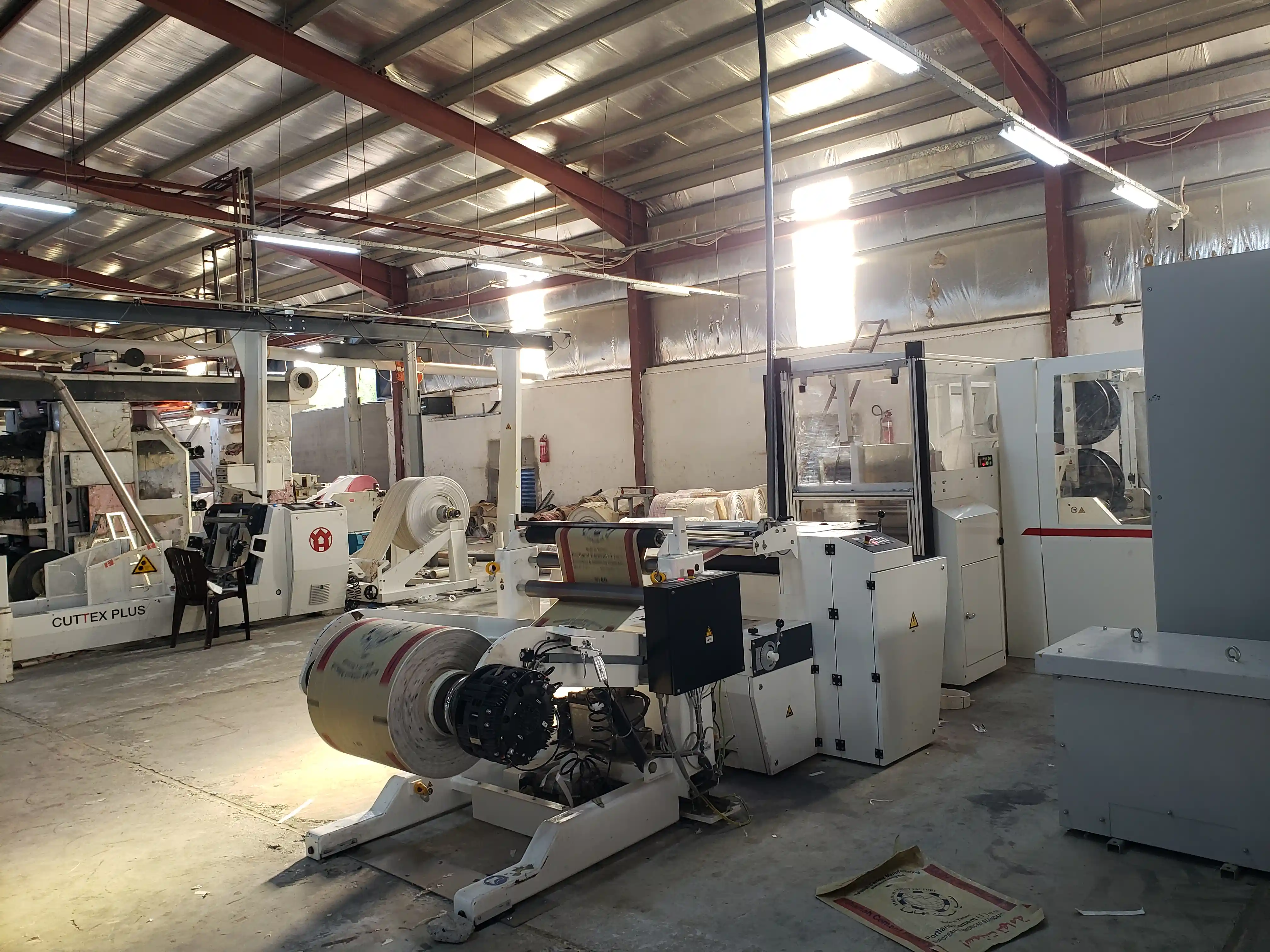
Step Three
The printing stage on woven bags at this stage woven bags are printed either on one face or on two sides with a maximum of four colors. The process depends on the installation of the eclachic cylinders according to the operating order or customer requirements with the required eclachean processing for printing, printing steps:
1. Equip the required inks and adjust her wife appropriately.
2. Installation of the fabric roll required for printing in the machine.
3. Start the printing process by accurately sitting colors on the bag at slow speed to ensure sample matching.
4. Raise the printing speed after stabilizing the edition to efficiently complete the process.
5. Monitoring the quality of the edition during operation to make sure there are no defects.
6. Stop the device and fix the problem in case of any fault in the edition.
7. Cut the printed roller after finished printing the fabric roller and install the new roller for printing.
8. Move the printed roller to the next stage which is chopping and sewing.
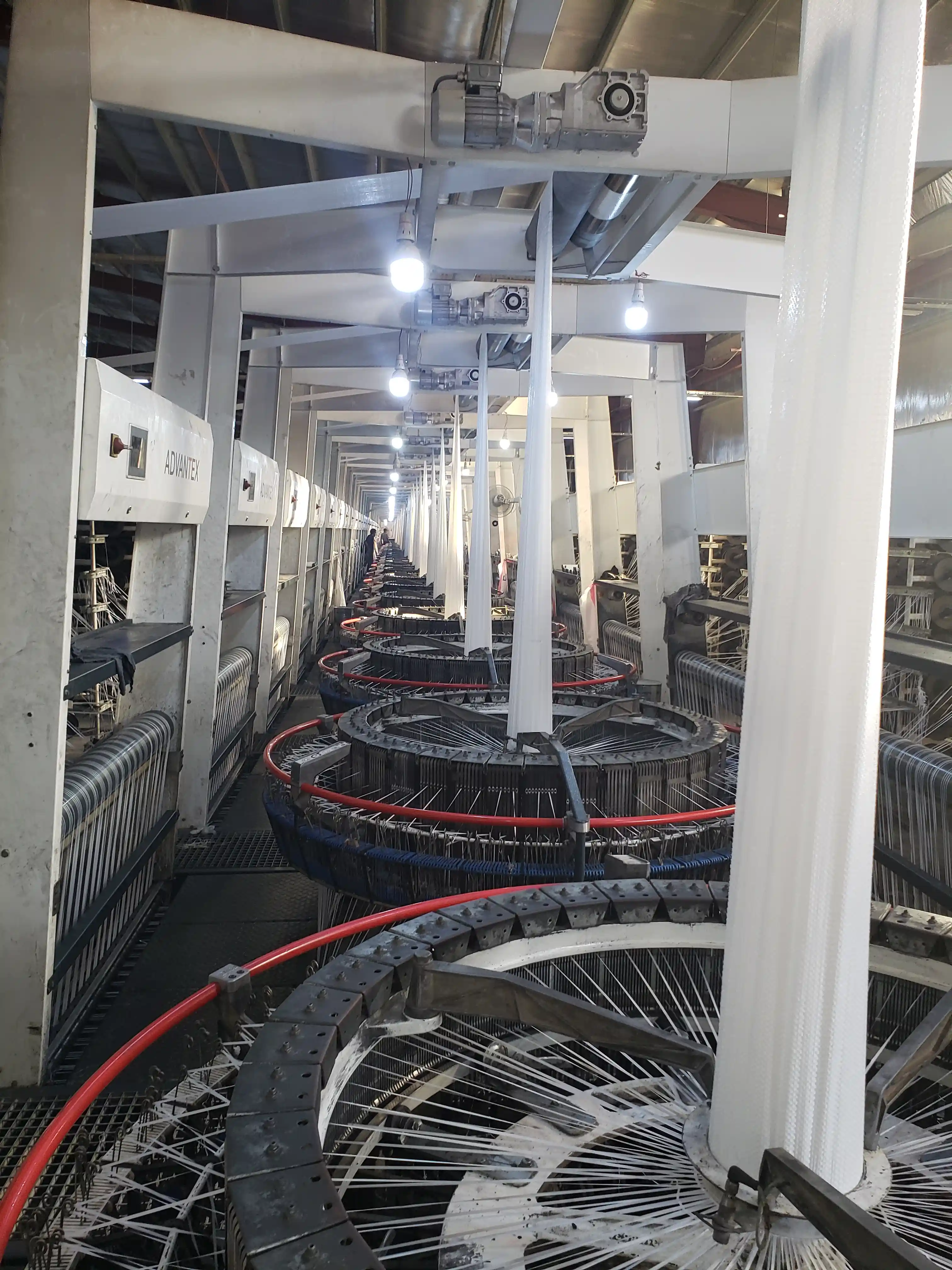
Step Four
The cutting and sewing phase at this stage printed rolls or net rolls (which do not contain printing) are cut into bags. Bag specifications, operating conditions and number of bags per stack are entered into the computer. After that the machine cuts the bags, then the bags are pulled into the sewing machine to pass the sewing process. Once the sewing is finished, the bags are transferred from the cutting and sewing stage to the plunging stage. At the capping stage, bartender-shaped bags are arranged where each pendle contains 500 bags. The machine is also fitted with a vibrator to ensure that the bags are strictly and effectively regulated.
Step Five
The piston stage in which the bartenders are pressed and tied each pendle 500 bags and transported on wooden drums to be delivered to the complete production stores and from them to the customer.
Step Six
The manual sewing phase in which the defective bags are re-stitched, assembled and counted on the image of a bartender and transported for taping or to cutting and sewing to complete a deficient bartender as well as can sew the lining bags (poly ethylene bag inside the proplin bag) or sew a passion from the top of the bag.
Step Seven
The Recycle phase is the machine of returned materials in which the scrape is recycled and converted into granules for reuse by floss lines in which the scrape is sorted and checked from impurities before it enters the machine's course and from it to the mill and then pulled by the sacro after it is warmly dissolved the heaters mounted on the extruder and then the cutting knife is converted into granules and then pulled to the tank.